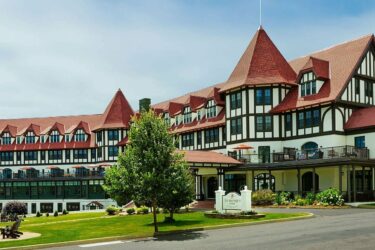
InnVest Hotels acquires The Algonquin Resort St. Andrews by‑the‑Sea, Autograph Collection and The Algonquin Golf Course
InnVest Hotels has acquired The Algonquin Resort St. Andrews by-the-Sea, Autograph Collection and The Algonquin Golf Course.
When builders, developers and architects are looking to make the best use of income-generating space for mixed use commercial projects streamlining parking space is especially when land is limited or expensive.
By Del Williams
For developers and architects, maximizing income-generating space for mixed use commercial projects is critical, particularly when land is limited or expensive. In many cases, the project cannot advance unless the architect can somehow “create space” to achieve the building design and parking density required.
Traditional parking garages, however, waste valuable real estate due to their inefficiency in storing vehicles. As a solution, advanced automated parking systems allow developers and architects to store from two to four times the number of cars on the same land by eliminating the need for drive aisles, ramps, and space for car doors to open. This provides industry professionals with more options to design projects that can maximize revenue-producing square footage that increases total project value.
Although such technology has been used for several decades overseas, particularly in European urban centers, it has been refined and improved over the last 20 years in the United States. Today, more sophisticated systems are able to park and return 400+ vehicles per hour if designed to do so, which minimizes potential wait time during periods of peak demand. These systems are also designed to deliver unprecedented reliability with 99.99 per cent uptime and failsafe redundancy, making them a more viable option than ever for incorporation in building development plans.
Such advanced automated parking technology was essential in helping Gary Tave, a licensed engineer, building contractor, and owner of Square Peg Development LLC. Tave sought to develop a $49 million mixed-use project, called West Bay Lofts, on two city blocks in downtown Largo, Florida. The project, which is a key component of revitalizing the downtown area, will include 123 market-rate apartment homes and 40,000-square-feet of ground-floor commercial space in two structures.
Early on, however, the project’s feasibility was in question, primarily due to a lack of needed parking, and spiraling high-rise construction costs that would be required to add the parking required.
“With the project’s constraints in property setbacks, height restrictions, and optimization of net leasable square feet against construction costs, I realized there wasn’t enough available square footage to meet all of the zoning criteria using conventional construction technologies,” says Tave. “The main limiting factor was available parking.”
But when Tave explored purchasing additional land to accommodate a parking structure, he found it was not allowed due to municipal priorities. “We were not able to acquire a piece of adjacent land because the city did not want a large parking lot taking up valuable space downtown,” he says. “So, conventional parking was not an option.”
According to Tave, he also considered adding stories to the building to accommodate several layers of parking. However, this would require building to high-rise construction safety requirements. This would add 25-30% to costs, making the project too expensive to pursue.
Profitably Optimizing Development Space
As a solution, a growing number of developers like Tave – as well as architects worldwide – are turning to automated parking garages to cost-effectively “free up” space.
Tave says in his prior experience and travel overseas, he had seen mechanical parking solutions. However, the mechanical stackers he had seen in Manhattan, New York, for instance, were not sophisticated and required too many ‘manual valets’ and too much maneuvering space, which was not economically feasible for the project.
When doing Internet research, Tave discovered Robotic Parking Systems, an advanced automated parking technology, by a Clearwater, Florida-based manufacturer of the same name. Before determining that the current technology suited his project’s goals, he was determined to first do his due diligence. As a retired Navy Civil Engineer Corps Commander, he drew on his almost 25 years of active duty service, spent dealing with issues of real estate acquisition, development, management, disposition, and building project life cycles.
Compared to previous forms of automated parking, the advanced technology provides more reliable and consistently faster vehicle delivery. This is due to a unique design that can independently move dozens of vehicles simultaneously on electro-mechanical robotsin three axes (left-right, forward-back, and vertically). The result expedites automated parking and retrieval even in periods of peak demand.
In this type of system, vehicle owners drive into a street-level “terminal” at the automated garage, turn off the vehicle and exit with their keys. Then sophisticated software controls, platforms, lifts, motors, sensors, and other mechanical gear transport the vehicle to an open slot in a multi-story steel shelving system. Different sized bays accommodate larger vehicles, such sedans and SUVs, to improve space utilization. When the owner wants to leave, the system locates the vehicle and returns it to a ground level exit terminal.
Less responsive older systems typically utilize only one or two devices such as trolleys to move vehicles. However, these can become intolerably slow and unresponsive during periods of peak demand, so are not well-suited for high-volume parking environments.
“What matters in today’s robotic parking systems is not how long it takes to retrieve one single car, but how long it takes to retrieve ten cars when ten people are waiting,” explains Tave. The multiple exit paths and sophistication of Robotic Parking Systems’ programming helps to quickly get vehicles to their owners.”
Tave was also impressed with the implementation of the technology at the Al Jahra Court Complex in Kuwait, which recently earned the Guinness World Record for the “Largest Automated Parking Facility.” It was designed as a combination of 684 concrete ramp parking spaces with 2,314 automated spaces on top. The Robotic Parking Systems portion of the project provides almost 3.5 times the number of conventional ramp-style parking spaces in approximately the same volume. While the conventional parking portion is 7 levels and over 97 feet high, the RPS portion is 11 levels and 115 high.
The Robotic Parking System in the Al Jahra Court Complex can deliver almost seven cars every minute. It has a certified peak traffic throughput of 425 cars per hour inbound/outbound, delivered through the 12-grade level entry/exit bays that service the garage. Average retrieval takes 177 seconds.
Establishing the technology’s reliability, of course, was also a crucial concern because it would need to function under any and all circumstances.
To satisfy himself in regards to the automated parking technology, Tave says he drew on his lifetime of engineering expertise to independently review the specifications of all the equipment from the servo motors to the network servers. He also did his own independent due diligence by researching the suppliers of the system’s components.
What Tave found satisfied his demand for the utmost system reliability.
“There is a significant difference between systems with single machines operating in multi-dimensional modes, and the Robotic Parking Systems design where each direction of vehicle travel is handled by a separate piece of equipment with redundancy built into every facet of the system, including the server that operates it,” says Tave. “With the latter, you can achieve exceptionally high levels of reliability.”
In fact, Robotic Parking Systems historically perform with 99.99 per cent uptime on a 24/7 basis. This track record started in 2002 and continues today. The system utilizes electrical and mechanical components with lifespans of 40,000 hours or more, and incorporates true redundancy of components throughout the entire system.
In the automated parking facility, every machine has built-in redundant components, and at least two of each type of machine is installed. Each of the redundant machines can simultaneously perform the same tasks, so if one needs maintenance or repair, the other is always available to keep vehicles moving in and out of the garage. In terms of data processing, an industrial server designed for 99.999% uptime, paired with an identical redundant automatic hot swappable unit, provides failsafe reliability.
While the initial cost of such a reliable automated parking system is higher than a traditional concrete garage, it is offset by lowering total development costs (including land, construction and soft costs) by as much as 40 per cent. Typically, only half the space is required for the same amount of parking, which can significantly reduce the outlay for land purchase. Or, alternatively it can increase the revenue generating development capacity on a given piece of land.
The modular automated parking systems can also provide developers and architects needed design flexibility. The parking structures can be built above ground, underground, inside a building, on top of a building, or under a building. Any type of facade can be used whether half-timbered, brick, aluminum, concrete or glass. This enables architects to seamlessly blend the parking structures with the project or neighborhood.
Based on a thorough technical/financial review of the technology, Tave is incorporating a Robotic Parking Systems design with 470-vehicle capacity and 240 vehicle per hour throughput in the West Bay Lofts project.
Because the automated parking garage will be embedded in the building’s core, surrounded on all four sides by apartments with active balconies, there will not be any “ugly industrial” side of the building. Vehicles will depart through stylish exit bays in the north side of the building.
The West Bay Lofts project recently broke ground, and completion is expected in February 2021.
“The automated parking system is key to making our development project feasible and is the first thing everyone wants to talk about. It gets a lot of attention from the media, politicians, and interested customers which helps our sales and marketing,” he concludes.
For more info: call 727-539-7275; Fax 727-216-8947; email info@roboticparking.com; visit www.roboticparking.com; or write to Robotic Parking Systems, Inc at 12812 60th Street North, Clearwater, FL 33760.
Del Williams is a technical writer based in Torrance, California.
He writes about health, business, technology, and educational issues, and has an M.A. in English from C.S.U. Dominguez Hills.
InnVest Hotels has acquired The Algonquin Resort St. Andrews by-the-Sea, Autograph Collection and The Algonquin Golf Course.
The new owners of the famed Windermere House hotel and resort on Muskoka’s Lake Rosseau intend to revitalize the building and its amenities while preserving the property’s historical integrity.
Proactive Hospitality has acquired the Coast Osoyoos Beach Hotel, B.C. CFO Capital arranged acquisition financing for the deal.
Tribute Portfolio – part of Marriott Bonvoy's extraordinary portfolio of 31 hotel brands – continues to grow its global family of characterful hotels with Honeyrose Hotel Montreal, a Tribute Portfolio Hotel, the brand's…